How to improve production efficiency: The order is cleaned up to the entry point to investigate as the core!
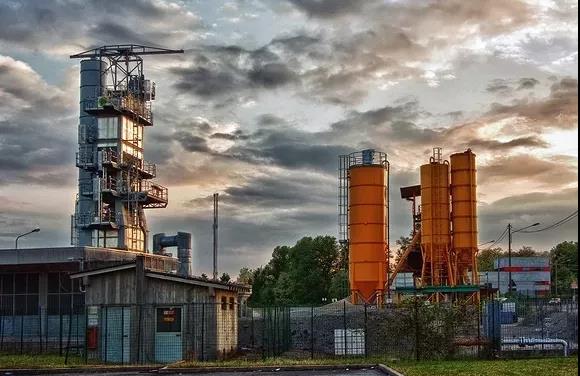
Business background
1. This company is a manufacturer specializing in the production of computer headphones. In 2004, in Shenzhen investment plant, it is developed at home and abroad. It has developed 40,000 square meters, 25 production lines, and has more than 1,000 proficient workers and managers. Name, monthly output value of about 12 million headphone manufacturing plants.
2. Current status 1. Order review management is out of control, buried "scourge", order processing management, order processing, leading to production cycle, reducing the order transaction rate, affects shipping delivery and business orders.
3, status quo 2, plan management is extensive, no true sense to download the production day; the plan did not do full investigation before, the plan did not truly guide, coordinate the role of production, the plan is not to do, the plan is in the form .
4, status 3, the material procurement cycle is relatively long, and the amount of material is low in time. Storage management is confusing, the material is used exceeds the standard, the supply is not smooth, and the material accounts are not actually.
5, status 4, production arrangements are unreasonable, not prepared, check, equipment maintenance movement is not in place, visualize management is done, abnormal treatment is not timely, production efficiency is low.
6, status 5, abnormal material quality is frequent, data statistics distortion; the first management is extensive; the process inspection management is out of control, abnormal improvement measures are not perfect, analysis and improvement activities.
Please talk about your views and solutions in accordance with the status quo of the above enterprises, to achieve the purpose of improving production efficiency.
Solutions
Customized as the entry point to investigate as the core, awareness of the overall situation of the order;
First, data statistics:
Analysis of existing orders, currently not completed order 597, 457 outlets, accounting for 76.55% of the total number of orders, the translation rate is only 23.45%;
Second, the process card:
1. Sir "Production Plan Operation" related procedures, use "prior to push the pull" idea to find out a model suitable for enterprises "production plan operation" mode.
2. Crack the product process operation map and combine the current efficiency data analysis to assemble, packaging workshop as critical control nodes, import the day plan action;
Third, the plan chain action is implemented:
1. Optimize and consolidate the "Order Review Form", promote the standardization of "order review", can effectively prevent and reduce the incidence of "process abnormalities";
2. Establish "Order Decomposition Decomposition Table", order tasks are subdivided in production time, subdivided to all links, unify the goals, and make a paving for the production plan;
3. Develop, implement the "main production plan", through the "main production plan", fully understand the status of the order;
4. On the development of the "Order Cleanup Project", set the monthly phase of the target, summarize, review, and solve the problem of expired order backlog;
5. Establish a "Package Package (Cold Rolling) Day Plan" "Group Bank (Cold Rolling) Day Plan" "Packaging Workshop (Cold Rolling) Day Plan", focus on various functional department goals, and conduct investigations around the day plan, Ready to work;
6. Establish a "plan to achieve an assessment program", during the implementation of the "Day Plan", summarize and assess the procedure;
Fourth, the material chain action is implemented
1. Establish, optimize "Production Scheduling (Long-Term Rolling Plan)", will provide a basis for the production date, quantity, refinement to specific days, quantity, and information for property control, procurement and related department;
2. Continuously promote the "Procurement Day Plan" to optimize the "procurement plan to reach the assessment" method. The completion of the procurement plan is subjected to the day and week;
3. Formulate the establishment of "procurement control form", through this action specification and management procurement order progress, control material back to factory plan, while unfair, the stock is reasonably controlled;
4. Make an in and out of the deposit card, the position storage card, requires timely update card writing, clear date, name, specification, number of users, remaining quantity and signing confirmation, and requirement with the physical phase rate, and put it in the designated area;
5. In order to improve the phenomenon of raw warehouse material, it has been formulated the implementation of "position storage card", warehouse main channel / fire area adjustment plan, 6S training promotion skills, 6S joint inspection;
6. Develop a warehouse "daily explosion check table";
V. Scrolling troubleshooting:
1. Establish and import the "single meeting" mechanism to develop the "production pair meeting agenda". From PMC organization, procurement, production, audit, to form a "resolution" on the default part;
2. Layout multi-investigation to ensure the "Step Cold Roll Moving Day Plan"; set the "preparation annoyance", "defect report", clear online time, team;
3. Standardize and optimize the order, formulate and implement the "Coordination Conference Discipline" in the "Production Coordination Conference". Changing the "Coordination Conference" is free to spread, and there will be no decisions, and there will be no results;
6. Employee incentive:
1. Develop the implementation of "Raise BACK"
2. Improve efficiency to balance the pre-assembly of the assembly work. Before the production, the order is integrated, and the "pre-engine product capacity improvement plan" is formulated.
Implementation Effect
The order quasi-interest rate is increased by 52.54%;
Packaging per capita production is 55%;
Summarize
The promotion of production efficiency is first in the plan, the purpose of combing is the smooth flow of information, can quickly see the clearing, no problem, where is the problem, so, first, a "know" problem, first go "Know", this is a key point, because of the real knowledge, the problem will naturally be resolved.