In dry compounding of plastic film, edge sticking failure often occurs. The so-called edge sticking refers to the phenomenon that the plastic film is heated and dried by the drying trunk after being coated and glued, and then rolled up after being extruded by the hot pressing steel roller, and the two sides of the rolled up finished product are bonded together. After the edge sticking failure of the finished winding product, the film layers are firmly bonded at both ends of the winding material, which will make it difficult to separate the finished film. Especially when using two-component two-liquid reactive adhesive, it is easy to appear. In serious cases, it will also lead to the breaking and deformation of the composite finished product, resulting in the scrapping of the product, which is quite painful.
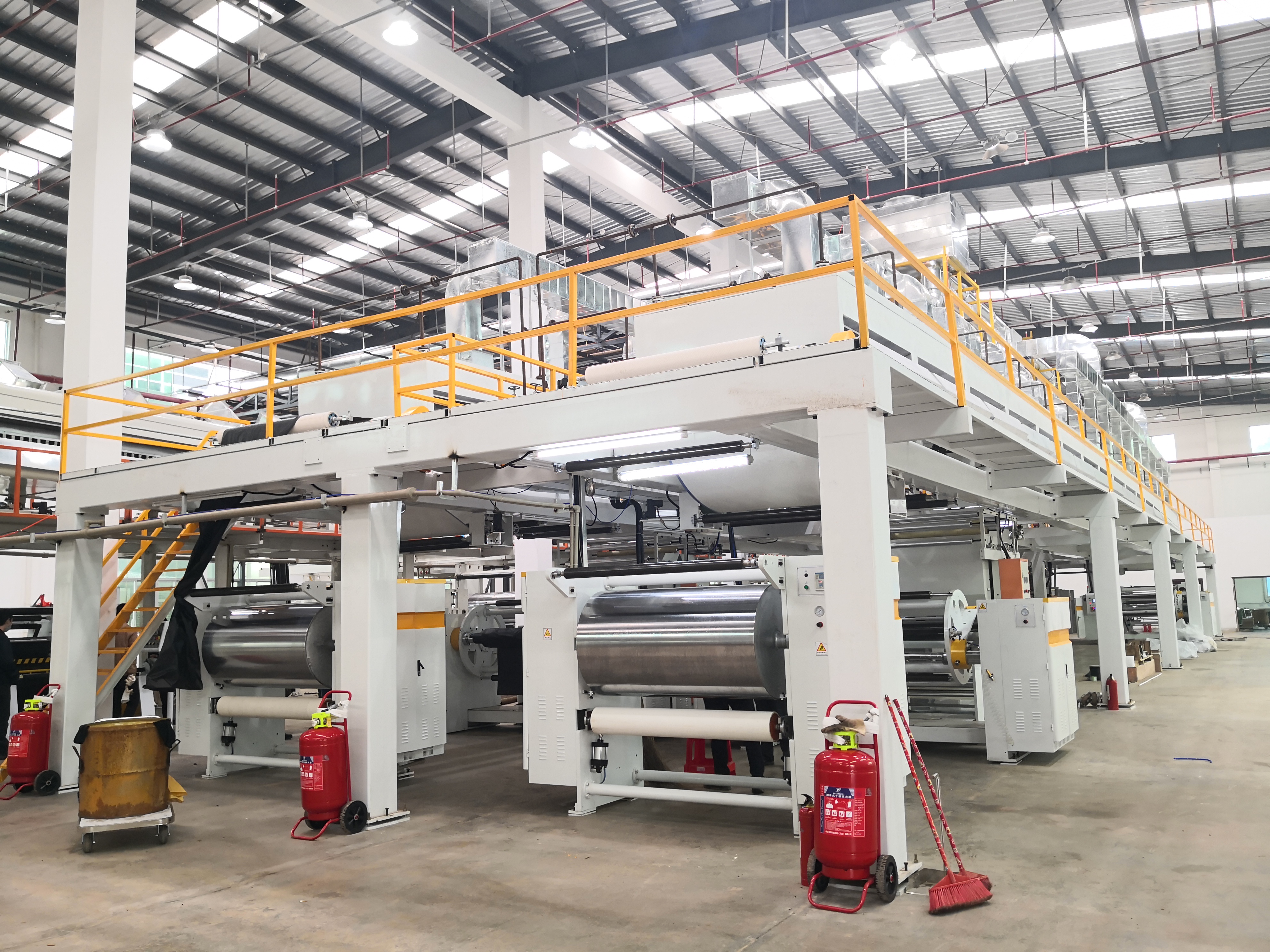
At present, the gluing system of compound machine used by many small printing enterprises is still non scraper type. The difference between the non scraper gluing system and the scraper gluing system is that the non scraper gluing system adjusts the gluing amount through the threaded rods at both ends of the gluing roller, while the scraper gluing system adjusts the gluing amount through the scraper and anilox roller.
If you want to achieve a faster and more efficient bonding function, you can wait and see the labor results of the machine as long as you adjust some switches and temperatures. Secondly, it can realize a repeated adhesion process, because the whole machine is heated and insulated. When some metal parts or other parts with special needs are adhered, it can realize the repeated adhesion process.
In addition, it can adhere a variety of materials, which makes it possible to put the hot melt adhesive coater into use in various industries, so this function is also widely respected and used by everyone.